3D Printing Phoenix turns digital CAD models into physical parts in hours, dramatically cutting design and production time. It’s used across all industries, from spare parts to jigs and fixtures and even end-use products.
The process involves building up layers of material to create an object; these can be a range of materials from plastics and metals to concrete and bio-materials.
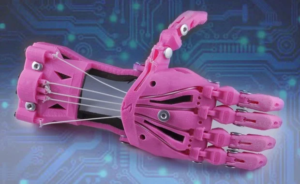
3D Printing is additive manufacturing, which creates physical objects from digital designs, layer by layer. This technology can create end-use parts or devices and has transformed many industries.
Several 3D printing technologies, such as selective laser sintering (SLS), powder bed fusion, electron beam melting, and stereolithography, use different methods to create thin layers of material. These layers then join together to make the final object.
The cost of 3D Printing is lower than traditional manufacturing techniques, making it a viable option for low- to mid-volume production. It can also reduce the time it takes for a product to get to market as it eliminates the need for expensive molds, which are required with injection molding or machining. In addition, 3D Printing can help reduce the number of components in a product, which can make it lighter and more efficient.
It’s also ideal for prototyping new designs and prototypes, which can be produced in-house rather than relying on supply chain logistics to ship samples to multiple locations. It can also be used to manufacture spare or replacement parts, which can help cut costs by avoiding costly shipping and handling charges.
Another useful application for 3D Printing is in the automotive industry, where it can be used to make tooling and jigs. For example, Pankl Racing Systems replaced machined jigs and fixtures with 3D printed parts, which decreased costs by 80-90 percent. In the future, it’s likely that more and more manufacturers will incorporate this technology into their design or production process. The companies that don’t will find themselves left behind. That’s because, as the technology continues to evolve, it will be able to offer even greater performance and precision with faster speeds.
How 3D Printing Works
In 3D Printing, also known as additive manufacturing, digital files are used to create three-dimensional solid objects through a layering method. In the 3D printing process, sequential layers of material are laid down by the ‘printer’ until the object is complete. The materials can vary in shape, size, rigidity and color.
First, a virtual design is made using computer-aided design (CAD) software. This type of software allows for precise drawings and technical illustrations. The design is then broken down into hundreds or even thousands of thin, horizontal layers. These layers are then stacked together to create the final part.
Depending on the type of printer, different methods are used to create the printed part. For example, laser-cured liquid resin is a common method for creating plastic parts, while fusing small particles of polymer powder creates metal parts. Some 3D printers use directed energy deposition to fuse the layers together, while others rely on material jetting. Some printing processes require a high level of precision and finish, while others are more forgiving and can handle slight deviations.
3D Printing allows for the creation of innovative geometries that would be difficult, costly, or impossible to produce with traditional manufacturing practices. For instance, organic shapes or overhangs can be printed, allowing for reduced weight and increased strength, while complex assemblies can be simplified into fewer parts to reduce costs, speed up assembly time and alleviate weak joints.
Many companies are taking advantage of the benefits of in-house 3D Printing, including reduced cost and shorter lead times. In addition, keeping production in-house can help companies avoid intellectual property concerns and maintain privacy. Another benefit of in-house 3D Printing is that it can allow organizations to quickly react to changes in consumer demand.
Materials
One of the biggest strengths of 3D Printing is its ability to create objects in a wide range of materials. The material you choose for your print will depend on its properties and the type of 3D printer you’re using.
Most common 3D printing materials are thermoplastics or ceramics. Plastics come in two forms: filaments and resins. Filaments are long strings of melted thermoplastic that a printer nozzle deposits layer by layer in the build area to form an object. Fused deposition modeling (FDM) 3D printers melt and extrude a range of thermoplastics including Polylactic Acid (PLA), Acrylonitrile Butadiene Styrene (ABS), and polypropylene (PP). Resins are liquid photopolymer plastics that cure or solidify when exposed to light. They are used in stereolithography (SLA) and digital light processing (DLP) printers.
Metal powders are another popular 3D printing material that offers strength, durability, and heat resistance. They’re often used for functional prototypes and end-use parts. Common metal powders include aluminum, titanium, and stainless steel.
Composite materials use polymers with added reinforcements to improve their properties. Carbon fiber is commonly used as an outer coating on plastics to give them enhanced strength, while glass and Kevlar are popular choices for engineering composites. There are also a number of composites that combine a polymer with other materials to give the prints unique visual or textural properties, such as wood and glow-in-the-dark plastics.
Sustainable materials are a growing trend in the industry, with companies developing biodegradable filaments and recycled plastics to reduce waste. Others are aiming for net-zero carbon processes that help to eliminate carbon emissions from production.
Software
There are a variety of software programs that can be used with 3D Printing. Some are specialized for design and modeling, while others help prepare the 3D model for Printing or provide tools to manage the printing process. Some also support multiple file formats and printers, making it easy to switch between different systems.
CAD software is essential for creating the initial digital model that will be printed. These computer programs have a wide range of features for drawing, sculpting, and modifying 3D objects. Examples of CAD software include AutoCAD, FreeCAD, and SketchUp.
Slicer software translates 3D models into the instructions a printer understands by converting them into G-code, a set of commands specifying toolpaths and movements. This software helps streamline the printing process and ensures that all print settings are correctly configured. It can also help reduce waste by enabling users to modify or adjust the size of objects and layer heights.
Hosting software enables users to monitor and control their 3D printers remotely. These programs can be used to load models, start or pause print jobs, and send status updates. They can also be used to create or save printing profiles, which are sets of parameters for each print job. This makes it easier to print complex and durable parts, reducing the amount of manual work required by removing supports or manually finishing prints.
For beginners, it is important to select a software that has an intuitive interface. Look for options known for their ease of use and extensive library of shapes. This can make the difference between a difficult and smooth transition into the world of 3D Printing. It is also useful to read online reviews and try out some of the available software before making a final decision.
3D Printers
3D Printing is a flexible and cost-effective manufacturing method for prototyping and low- to mid-volume production. It complements and sometimes replaces traditional injection molding or machining for a growing range of end-use parts.
Before a 3D printer can print a physical object, it must create a virtual design of that object. This is done using a type of software called computer-aided design (CAD). This software works like a blueprint, creating a precise representation of the final product. It then breaks the model down into hundreds or even thousands of thin layers for the printer to use.
These layers are then deposited onto the print bed by the printer’s nozzle in a process similar to how an inkjet printer creates text or images on paper. As the layers are deposited, they stack one on top of another to form the desired object. 3D printed objects can be made from a wide variety of materials. Some are made of polymers, such as plastics, which are strong and tough to break. Others are made of a more durable and lightweight metal, such as titanium or carbon fiber. Lastly, there are composite options that combine a polymer with fibers of other materials to give them specific properties such as strength or flexibility.
The result is a finished part that can be used in the same way as other manufactured parts. However, it may still require additional processing such as priming, painting or fastening. In some cases, these components are fabricated alongside traditional products in production lines. For example, Pankl Racing Systems has replaced machined jigs and fixtures with 3D-printed versions, cutting costs by 80-90 percent. Medical professionals are also now able to print models of patients’ organs before surgery, giving doctors the chance to practice on them first.